Ndfeb hydrogen decrepitation.jpeg.
Abstract. This paper reports the desorption of hydrogen from NdFeB powder, and unmilled material, produced using hydrogen decrepitation as a pre-milling technique, investigated using a mass spectrometer to monitor the hydrogen partial pressure in the system as the sample was heated under vacuum from room temperature to …
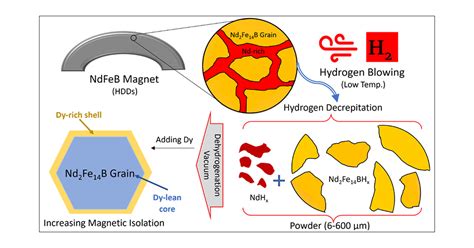
The behavior of hydrogen absorption in the NdFeB Hydrogen Decrepitation process is affected by the shape of the NdFeB alloy, pressure and temperature curves of the reaction process, which makes the reaction process with characteristics of nonlinear, time-varying parameters and coupling. In this study, we proposed a state space modeling …Feb 1, 1997 · Hydrogen decrepitation of Nd-Fe-B type magnet alloys is a two stage process. Firstly, the hydrogen reacts with the Nd-rich phase at or close to room temperature. This is an exothermic reaction [4] and the heat evolved then allows the second stage to proceed in which the hydrogen is absorbed by the Nd^FeuB matrix phase. NdFeB ingot exposed to hydrogen atmosphere due to the changes of hydride lattice parameters cracks. The process called HDDR (Hydrogenation - …Sintered Nd-Fe-B magnets were subjected to the Hydrogen Decrepitation (HD) process at various temperatures in the range of 50-300°C, at two different pressures, 50 kPa and 200 kPa, followed by ...The use of 3-D laser confocal microscopy to visualise hydrogen interactions in-sit; The use of hydrogen decrepitation to extract NdFeB magnets from electronic assemblies; In-situ removal of magnets from large magnetic assemblies using hydrogen; Corrosion protection for NdFeB magnets; Recycling of rare earth magnets; Strip casting …
Rare earth magnets based upon neodymium-iron-boron (NdFeB) are employed in many high tech applications, including h... Skip to main content. Sign In Create account . Journal Article OPEN ACCESS. THE USE OF THERMAL HYDROGEN DECREPITATION TO RECYCLE Nd-Fe-B MAGNETS FROM ELECTRONIC WASTE. Piotrowicz A; Pietrzyk S; …Dec 20, 2020 · Extraction of NdFeB from rotors using hydrogen. Seven semi-embedded rotors and non-embedded rotors were processed separately in two experiments. All the magnets in individual slots were scored in concentric circles using an angle grinder to provide a fresh surface for the hydrogen, as shown in Fig. 3, 15–30 min before being loaded into the ...
In this paper, the hydrogen processing of scrap magnets has been demonstrated as an extraction method for NdFeB from automotive rotors for the first time, with the aim to …Hydrogen Decrepitation (HD) has been used as an efficient and economical method in producing coarse NdFeB powder. This article studied the effects of hydrogen on the Nd-Dy-Fe-B magnets, such as HD ...
Introduction. In the fields of sintered magnets, the hydrogen decrepitation (HD) technique has been widely used. The as-melted NdFeB bulk material becomes brittle after HD and decrepitates into powders, as a result of the large volume expansion of the lattice of both the Nd 2 Fe 14 B matrix and the intergranular Nd-rich phase [1]. Hydrogen …Oct 25, 2015 · End-of-life NdFeB magnets are important secondary RE sources. Several recycling methods for NdFeB magnets have been developed, such as direct reuse,4 hydrogen decrepitation (HD) and regeneration of new NdFeB,5–7 pyrometallurgical methods,8,9 hydrometallurgical methods,10–13 gas-phase extraction. magnets. The thermal and mechanical impact of the hydrogen decrepitation process was assessed during hydrogen processing. For all forms of sintered NdFeB scrap the surface condition of the magnets is important as oxidation has been shown to inhibit the onset of the hydrogen decrepitation process. In this Fully dense sintered NdFeB-type magnets have been subjected to the hydrogen decrepitation (HD) process. The resultant powder has been subsequently processed in one of two ways in order to produce ...
The influence of the alloy granulation grade, temperature and surface oxidation on the kinetics and the course of the fracture processes during the hydrogenation of Nd16−xDyxFe76B8 (x=0–3) alloy was studied. The average particle sizes of the alloy were 1 mm, 5 mm and 3 cm and the temperature range between 20 and 200 °C. Pre-oxidation …
Hydrogen absorption/adsorption properties of high coercivity NdDyFeCoNbCuB sintered magnets were determined. Hydrogenation kinetics were analyzed using both differential scanning calorimetry (DSC) and X-ray diffraction (XRD). Hydrogenation of the Nd-rich intergranular phase results in a rather broad and large peak …
Nov 15, 2021 · After the hydrogen decrepitation process, the powders were pulverized by either He-jet milling or N 2-jet milling, obtaining a powder with a particle size of ~0.8 µm for the HDDR processed and He-jet milled sample, ~1.0 µm for the He-jet milled sample, and ~3.0 µm for the N 2-jet milled sample. Novel hydrogen decrepitation behaviors of (La, Ce)-Fe-B strips. Jiaying Jin G. Bai +4 authors M. Yan. ... Doping with Dy/Tb is a current solution to improve the coercivity and the operating temperature of NdFeB magnets, by increasing the magnetocrystalline anisotropy of the (Nd, Dy/Tb)2Fe14B (2:14:1) …In recent years, under the background of global low-carbon development, the production of NdFeB magnets has increased dramatically. With the end of magnet life, a large number of discarded products will be produced in the future. At the same time, 6–73% of industrial waste will be produced in the manufacturing process of magnets. The rare …The method combines hydrogen decrepitation (HD) disintegration of the initial magnet, powder sieving and the Press-Less Process (PLP), where hydride powder is sintered in a graphite mold. Coercivities up to 534 kA/m were obtained in porous samples based on powder size d < 100 µm. Adding a ball milling step resulted in full density …Hydrogen Decrepitation is a process step used in the production of Neodymium magnets to create extremely small grains in the material. Neodymium magnets must have very small grains averaging about 5 micrometers in order to have the best magnetic properties. But the grain sizes after casting are much larger than that, so they must be ground down ...
Hydrogen decrepitation (HD) is based on the selective synthesis of neodymium hydrides though the reaction of hydrogen gas with neodymium located in the Nd-Fe-B magnet. …The initial step for manufacturing NdFeB plated permanent magnets in this unit process is NdFeB alloying and strip casting. NdFeB alloy is composed of 72% iron, 27% neodymium, and 1% boron from boron carbide (Sprecher et al., 2014). In order to stop free iron from forming, a small amount of iron formed between NdFeB crystals, the alloy is ...Magnetic powders for sintered NdFeB magnets have been prepared by using an advanced processing method including strip casting, hydrogen decrepitation, jet milling and rubber isotropic press. The effects of Dy, Ga and Co addition on the microstructure and magnetic properties of sintered magnets have been investigated. By adopting a suitable …Originated by Professor Rex Harris, the hydrogen decrepitation method, which is used to reduce NdFeB alloys to a powder, is now ubiquitously employed in worldwide magnet processing.We report investigations on the processing by Spark Plasma Sintering (SPS) of RE2Fe14B (RE = Nd, Pr…) powders obtained by hydrogen decrepitation of …Hydrogen absorption and desorption characteristics for high coercivity NdDyFeCoNbCuB sintered bulk magnets were studied, by differential scanning calorimetry (DSC) measurement and hydrogenation kinetics measurement. The DSC measurements showed that hydrogenation of Nd-rich phase occurred in the temperature range of …
magnets from electrical and electronic equipment. These materials are then processed using hydrogen decrepitation to transform the NdFeB magnets into a hydrogenated powder. This powder can then be extracted mechanically from the obsolete devices, and can then be processed further to produce either sintered or bonded rare earth magnets. A combination of hydrogen decrepitation (HD) and jet milling (JM) has been used to produce powder for the processing of permanent magnets. The procedure has proved to be very successful for both Nd-Fe-B (Neomax) alloys and the ND-Dy-Fe-Nb-B high coercivity alloys. The magnets produced by the HD/JM process showed excellent coercivities when …
Oct 30, 2018 · The Hydrogen Decrepitation and the Hydrogen Disproportionation Desorption Recombination processes for the preparation and the recycling of the two industrially produced phases of SmCo alloys, SmCo5 and Sm2Co17, are reviewed. The effects of the chemical composition, the microstructure, the exposure time, the hydrogen pressure, and the temperature on the hydrogen absorption are discussed. The ... The decrepitation process and related changes in the sample temperature are analysed to explain the experimentally observed weight gain curve of a Nd–Fe–B sample due to hydrogen uptake. It is shown that the expansion of the specific surface resulting from decrepitation of the sample is the most important parameter controlling …The processing and characterisation of recycled NdFeB-type sintered magnets. M. Degri. Materials Science, Engineering. 2014. A study of the processing and characterisation of sintered NdFeB magnets made from recycled feed stock was undertaken. Initially the hydrogen decrepitated (HD) powder was investigated using two…. Expand.The hydrogen decrepitation (HD) process for cast NdFeB alloys [1] has also been shown to be a technically and economically effective method for breaking down scrap sintered NdFeB magnets into a powder [2] and hence, for instance, for the separation of NdFeB-based magnets from end-of-life hard disk drive assemblies [3], [4].magnets from electrical and electronic equipment. These materials are then processed using hydrogen decrepitation to transform the NdFeB magnets into a hydrogenated powder. This powder can then be extracted mechanically from the obsolete devices, and can then be processed further to produce either sintered or bonded rare earth magnets.The Hydrogen Decrepitation and the Hydrogen Disproportionation Desorption Recombination processes for the preparation and the recycling of the two industrially produced phases of SmCo alloys, SmCo5 and Sm2Co17, are reviewed. The effects of the chemical composition, the microstructure, the exposure time, the hydrogen …
The process of hydrogen decrepitation (HD), which is used in the primary production and recycling of Nd magnets, takes place at low temperatures, even at room temperature, so that the entire microstructure decomposes only in powder form and the grain size is reduced.
big drive towards recycling of NdFeB magnets due to supply constraints for rare earth metals. Workers at the University of Birmingham have previously shown that hydrogen …
Absorption and desorption of hydrogen by the permanent magnet material Nd 2 Fe 1 4 B have been studied using a microcomputer‐controlled, thermomanometric analyzer with an initial hydrogen pressure of approximately 1 bar. Primary absorption occurs in the range 200–300 °C and results in the formation of a stable hydride with …The nature of hydrogen decrepitation when applied to a cast Nd-Fe-B permanent magnet alloy has been studied by following the microstructural changes on polished surfaces of the material exposed to hydrogen at a pressure of 4 bar. The milling of the material decrepitated at a pressure of 10 bar has also been studied by determining …Hydrogen decrepitation (HD) of Nd-Fe-B cast alloys is widely used in the processing of sintered magnets. The oxidation resistance under air of alloy powder …big drive towards recycling of NdFeB magnets due to supply constraints for rare earth metals. Workers at the University of Birmingham have previously shown that hydrogen …Hydrogen decrepitation as a highly efficient and excellent crushing method is widely used in the preparation of NdFeB magnets. ... Expand. 1. Save. The processing and characterisation of recycled NdFeB based magnets. S. Adrwish. Materials Science, Engineering. 2013; The scrap magnets were turned into a powder using the HD process. …Anisotropic powder was prepared with precursor (NdDy)-(FeCoNbCu)-B sintered magnets by hydrogen decrepitation, desorption, and subsequent annealing treatment. The hydrogen desorption was performed in magnetic fields of 0, 1, 3, and 5 T. The orientation of tetragonal phase grains of the powder was evaluated from the …big drive towards recycling of NdFeB magnets due to supply constraints for rare earth metals. Workers at the University of Birmingham have previously shown that hydrogen …Hydrogen decrepitation (HD) of the sintered block was used to return the annealed material back into a powder [33]. During this step, the material reacts with hydrogen resulting in volume expansion of both the Nd-rich phase, at triple junctions and grain boundaries, and the Nd 2 Fe 14 B matrix phase [34]. This expansion leads to …The ultrafine magnet waste (particle size < 1 µm) contained around 50% rare earths mainly in the form of hydroxides as they are generated from the hydrogen decrepitation. The major phases in ultrafine NdFeB waste were Nd(OH) 3, Fe 2 O 3 and Fe phases. When ultrafine magnet waste was leached with hydrofluoric acid, all the iron …
Hydrogen decrepitation (HD) is based on the selective synthesis of neodymium hydrides though the reaction of hydrogen gas with neodymium located in the Nd-Fe-B magnet. …This way of powdering known as hydrogen decrepitation (HD) is a well-established stage of manufacturing technologies of sintered [2], [3] and bonded [4] Nd–Fe–B magnets. The interstitial hydrogen in the ferromagnetic Nd 2 Fe 14 B phase reduces significantly its anisotropy field H A. That is why desorption of hydrogen is necessary in …Hydrogen decrepitation process has been applied for the first time for the direct recycling of SmCo 5 magnets. Industrially produced sintered SmCo ... Nowadays, NdFeB magnets represent more than 90% of the REE permanent magnets production. But, SmCo magnets have much higher coercivity and better temperature resistance, and many experts expect ...Instagram:https://instagram. jizzbunkerrdk 03004quiz 6 1 similar figures proving triangles similarfly fi International Journal of Hydrogen Energy. Volume 24, Issues 2–3, 1 March 1999, Pages 257-261. Application of hydrogen vibration milling in theprocessing of NdFeB and (Nd, Pr)FeB permanent magnets. Author links open overlay panel R.S Mottram 1, V Yartys 2, P.W Guegan 1, I.r Harris 1. Show more. know your meme didnpercent27t i do it for youdollar400 cad to usd An essential information about history and applications of Hydrogen Decrepitation has been generally reported. Very important technical details about the HD route were summarized, as well as fabrication procedure of Nd16Fe76B8 permanent magnet. Some micro strucural of SEM images of hydride and sintered magnets were given to … ul6f A combination of hydrogen decrepitation (HD) and jet milling (JM) has been used to produce powder for the processing of permanent magnets. The procedure has proved to be very successful for both Nd-Fe-B (Neomax) alloys and the ND-Dy-Fe-Nb-B high coercivity alloys. The magnets produced by the HD/JM process showed excellent coercivities when …Hydrogen Decrepitation and Recycling of NdFeB-type Sintered Magnets. Miha Zakotnik, E. Devlin, +1 author. A. Williams. Published 2006. Materials Science, Engineering. Journal of Iron and Steel Research International. View via Publisher. Save to Library.Apr 15, 2022 · An effective and complete processing route for the recycling of sintered Nd-Fe-B scrap magnets was proposed. Sintered Nd-Fe-B magnets were subjected to the Hydrogen Decrepitation (HD) process at various temperatures in the range of 50–300 °C, at two different pressures, 50 kPa and 200 kPa, followed by vacuum dehydrogenation in the range of 720–820 °C.